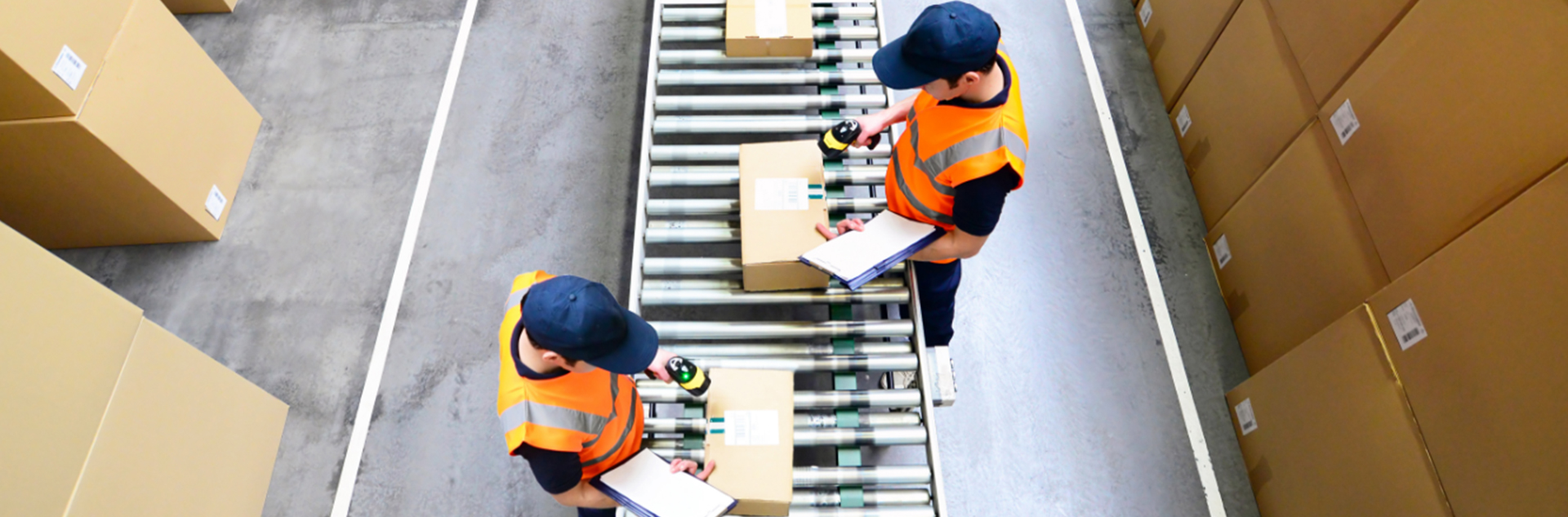
CUSTOMIZATION & OPTIMIZATION
Founder Weston Cook set out to reimagine the impersonal—and often impractical—3PL industry by starting a family-owned and operated 3PL company with homegrown values and an emphasis on serving local businesses with improved customization and optimization. Based in Livermore, Westhub Logistics serves both startups and big brands with a variety of fulfillment needs.

We’re Passionate About Customer Service
Our Promise
We believe taking the industry up a notch means bringing customer service back down to earth. Though we are small, we are mighty. And we believe our integrity is incomparable.
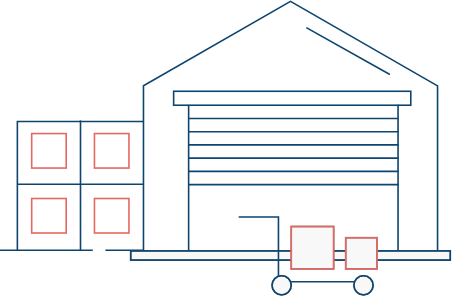
Our Team
We are here for you every step of the way. Meet the people who maintain an eagle eye on your business on your behalf.
With over 20 years of experience in logistics, transportation and delivery industries, Weston Cook founded Westhub Logistics, with the purpose of partnering with clients to meet their customers’ needs in the most cost-efficient manner possible. Prior, Cook founded and ran several large businesses in similar spaces. He enjoys spending time with his family and two dogs and hiking backcountry trails.
As Westhub Logistics’ Senior Sales Manager, Jessica Ramos is responsible for the company’s strategic development, growth and profitability. Prior to her current role, Jessica has held various leadership roles and helped accelerate operational support in sales/retail and new business development.
With a background in business development and project management, Emery Lykins has spent the least 20 years focusing on creating and implementing operational systems for a variety of businesses, small and large. Part of the Westhub team from the very beginning, Lykins brings a history of meeting customer expectations and maintaining positive client relationships.
Christine has over 20 years of experience in accounting administration and logistics. She is a valued asset to our team. She has a passion to manage and grow Westhub’s financial well-being. Christine provides her team with expert advice, professionalism, responsiveness and peace of mind. She enjoys spending time with her family if not driving the racetrack.
Sunita Chahal brings several years of diverse human resources and recruiting experience to the Westhub team. Prior, Chahal worked for corporate, retail and start-up companies, where she coordinated open enrollment plans, addressed employee issues, and trained and guided team members on the HR processes. She currently oversees all aspects of human resources practices and processes, including managing the complete employee lifecycle.
Dario Real is responsible for leading Westhub Logistics’ day-to-day warehouse operations. Real has 20 years of exceptional customer service, warehouse management, and logistical experience. Dario is deadline-driven and detail oriented. He is a professional leader adept in materials management and cost reductions. Possesses excellent organizational and problem solving skills.
Industry FAQs
Whether you’re new to the world of third-party logistics or you’re a long-time Amazon or Target seller simply looking to refresh your memory - the list of FAQs below are a great resource in understanding the terminology used within the logistics and fulfillment industry.
What is a Warehouse Management System?
A Warehouse Management System (WMS) is software designed to optimize warehouse operations, from receiving goods to shipping them out. It helps Bay Area 3PL businesses such as ourselves efficiently track inventory, handle picking, receiving, and storage, and ensures cost-effective movement of materials.
A WMS provides real-time visibility into inventory levels and can integrate with other systems like ERP, CRM, and TMS to streamline the supply chain. It aids in reducing labor costs, improving inventory accuracy, and enhancing overall efficiency.
For more information, visit this TechTarget article.
What is Cross-docking?
Cross-docking is a logistics strategy that removes the storage step in the supply chain. Products are unloaded from inbound transportation, sorted, and then directly reloaded onto outbound transportation for delivery, making the supply chain more efficient. For logistics companies on the West Coast, this is a game changer.
There are two main types of cross-docking: Pre-Distribution and Post-Distribution. In Pre-Distribution, goods are sorted and repacked according to pre-determined instructions before leaving the supplier. Post-distribution sorting is done at the distribution facility based on current demand and inventory needs.
The benefits of cross-docking include reduced inventory costs, improved delivery times, increased accuracy, better responsiveness, and increased sustainability. By reducing handling and storage time, cross-docking ensures faster delivery and less risk of product damage, giving retailers a competitive edge.
What Makes a 3PL Fulfillment Warehouse Different from Other Warehouses?
A 3PL fulfillment warehouse is a logistics facility specializing in handling logistics for other companies, primarily focusing on e-commerce. Unlike standard warehouses that simply store products, 3PL fulfillment warehouses manage the entire process of packing and shipping orders. They also handle inbound freight, storage, kitting, returns processing, and inventory management.
The key differences between a 3PL fulfillment warehouse and other warehouses include the range of services offered and the client base served. While 3PL warehouses cater to multiple clients, processing online orders and shipping directly to consumers, distribution centers typically serve single companies (such as Amazon or Target) and redistribute goods to brick-and-mortar stores.
What software do logistics companies use?
Logistics companies use various software solutions to manage their operations efficiently. These include logistics management software that covers order management, freight forwarding, trucking, and tools for managing shipments throughout the supply chain. Key types of logistics software include warehouse management software (WMS), supply chain management software (SCM), transportation management software (TMS), route optimization software, and driver and vehicle management software.
These systems help coordinate the delivery of goods, manage inventory, and optimize routes to ensure timely and accurate transportation operations. Many 3rd party fulfillment and logistics providers also use cloud-based software for better data security, scalability, and real-time updates. To learn more about Westhub Logistic’s state-of-the-art warehouse management and processing systems, visit our technology page.
How can E-commerce Companies Benefit From the 3PL Business Relationship in California?
E-commerce companies benefit significantly from partnering with third-party logistics (3PL) providers in California. These logistics companies offer a strategic advantage due to their proximity to major ports and airports, facilitating cost-effective and efficient transportation of products entering the United States from overseas. This ensures that goods are ready for distribution in the shortest possible time frame.
3PL providers in California offer comprehensive services, including warehousing, pick and pack, assembly, order fulfillment, labeling, packaging, shipping, and transportation management. These services streamline the supply chain, reduce operational costs, and enhance delivery efficiency. Additionally, 3PL companies provide value-added services tailored to meet the specific needs of e-commerce businesses. By leveraging these services, e-commerce companies can focus on their core business while relying on expert logistics partners to manage their supply chain operations.
What Is E-Commerce Fulfillment?
E-commerce fulfillment is the process of receiving, storing, picking, packing, and shipping products to customers. It’s a critical part of the supply chain that ensures online orders are delivered accurately and on time. Successful e-commerce fulfillment involves several key steps: receiving bulk goods, placing items into inventory, picking and packing orders, shipping them to customers, and managing returns.
A well-executed e-commerce fulfillment strategy is essential for customer satisfaction and business growth. By outsourcing to a third-party logistics (3PL) provider, e-commerce companies can streamline their logistics, reduce shipping costs, and focus on core business activities.
What Is Inventory Management and How Does It Work?
Inventory management is the process of determining the right quantity and timing for ordering stock, tracking inventory from purchase to sale, and responding to trends to ensure there is always enough stock to fulfill customer orders. It aims to balance the costs of holding inventory against the benefits of having enough stock to meet customer demand.
Effective inventory management helps companies maintain the right level of stock, minimizing the risks of stockouts and excess inventory. It involves various techniques and software systems to track inventory throughout the supply chain, from suppliers to production to customers.
The process includes receiving goods, storing them efficiently, picking and packing orders, and managing shipping and returns. By using inventory management software, companies can track the flow of products, optimize stock levels, and improve cash flow. This enhances customer satisfaction and drives business growth. For more information, visit this Net Suite article.